Free forging is a kind of simple, flexible metal forming method, while for small and medium-sized forging batch or under the condition of mass production, the free forging is recognized an obsolete, not economic forging forming method, but for small batch production or unit, especially large forgings, conducted on hammer and hydraulic press free forging, but still is a kind of suitable and economical production methods.
Die forging is the main forging process, the main equipment used are die forging hammer, anvil hammer, crank press, screw press and high-speed hammer. Die forging high productivity, forgings size stability, high material utilization rate, so widely used in forgings batch and mass production. It is estimated that the number of die forgings is large, accounting for about 90% of the total weight of forgings.
In fact, in addition to the basic methods of free forging and various die forging, there are some other special forming methods, such as electric upsetting, cold extrusion, rotary forging, roll forging, rotary forging, rotary forging, rotary forging, rotary forging, rotary forging, rotary forging, rotary forging, multi-hammer forging, magnetic forging, superplastic forming, hydrostatic forming, suspension forging, etc., which have developed very fast in recent twenty years at home and abroad. This kind of special forging technology will strongly promote the rapid development of material processing industry.
For forging furnace in forging plant, the detection and control of various thermal parameters is an important measure to improve combustion, reduce energy consumption, ensure technological requirements, and improve product quality and output.
Control fuel combustion, achieve furnace temperature, air - fuel ratio control. Pulsed combustion technology has been widely used in recent years. The pulse combustion controller takes the high speed burner as the control object, when the fuel quantity changes, guarantees the ejection gas high speed flow. Change quantity control time control, with small fire as long fire, with control fire output time to control the temperature rise rate. This control mode is in the opening of the furnace debugging will be small fire, fire combustion of the air/fuel ratio can be set appropriately, heating process does not need dynamic control of the air/fuel ratio, only to control the fuel and combustion air pressure stability, which greatly simplifies the control system composition, reduce the cost of furnace construction. However, the deviation between the actual furnace temperature and the set temperature is large in the pulse-controlled high speed combustion system. The deviation between the furnace temperature and the set temperature will be significantly reduced if the pulse time is shortened.
The fuel combustion control method mentioned above has been widely used in the production process. Through practical verification, the combustion control method mentioned above can effectively improve the fuel combustion condition, provide favorable conditions for the automatic control of other thermal parameters of the furnace, and meanwhile save fuel and improve the thermal efficiency of the furnace.
Control furnace temperature curve. On the basis of controlling fuel combustion, the furnace temperature curve (process heating curve) is controlled.
Control furnace pressure. It can ensure the stability of the furnace working condition, reduce the suction of cold air into the furnace, resulting in lower furnace temperature or furnace fire phenomenon. The sealing of furnace door, furnace car and furnace body is the difficulty of flame furnace sealing. The application of aluminum silicate fiber provides favorable conditions for solving furnace sealing. The soft and elastic characteristics of aluminum silicate fiber are used to make a rigid and flexible sealing surface, which is pressed by spring or cylinder to make the furnace a sealing body. Furnace sealing is the prerequisite and condition to control the stability of furnace pressure.
The furnace controlled by computer should have some basic conditions, such as advanced combustion device, recovery of waste heat, reasonable furnace body structure and building materials, otherwise it will not get satisfactory results even if it is controlled by computer.
Computer process control of industrial furnace is one of the effective measures to improve heating quality, reduce environmental pollution, save energy and improve production management. Now many forgings factories use industrial computers to achieve comprehensive management of the production process, man-machine dialogue, received very good results.
here are real pictures of our free forgings products, welcome to know more about us:
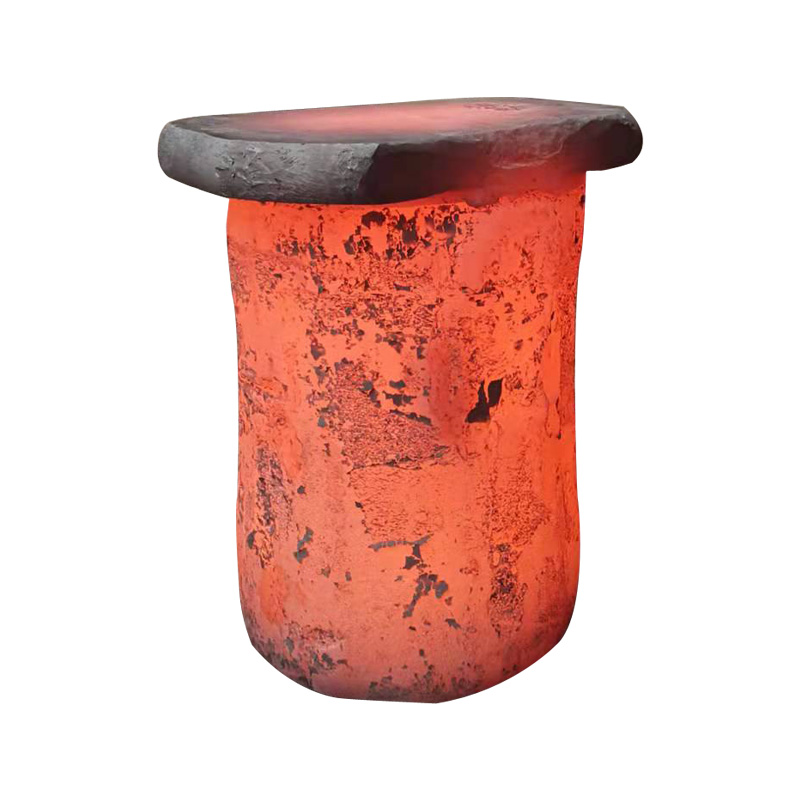
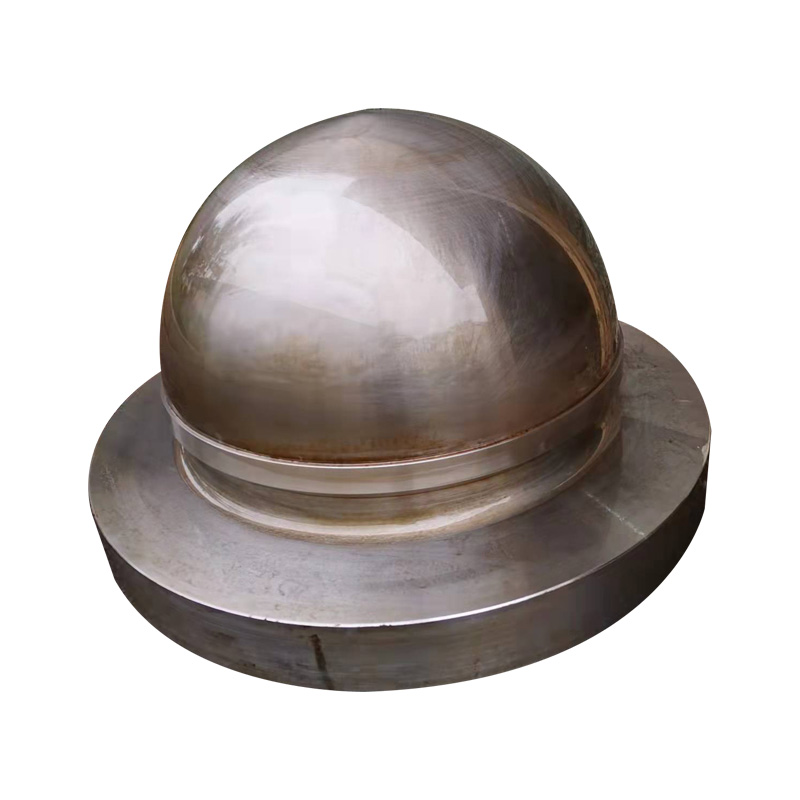
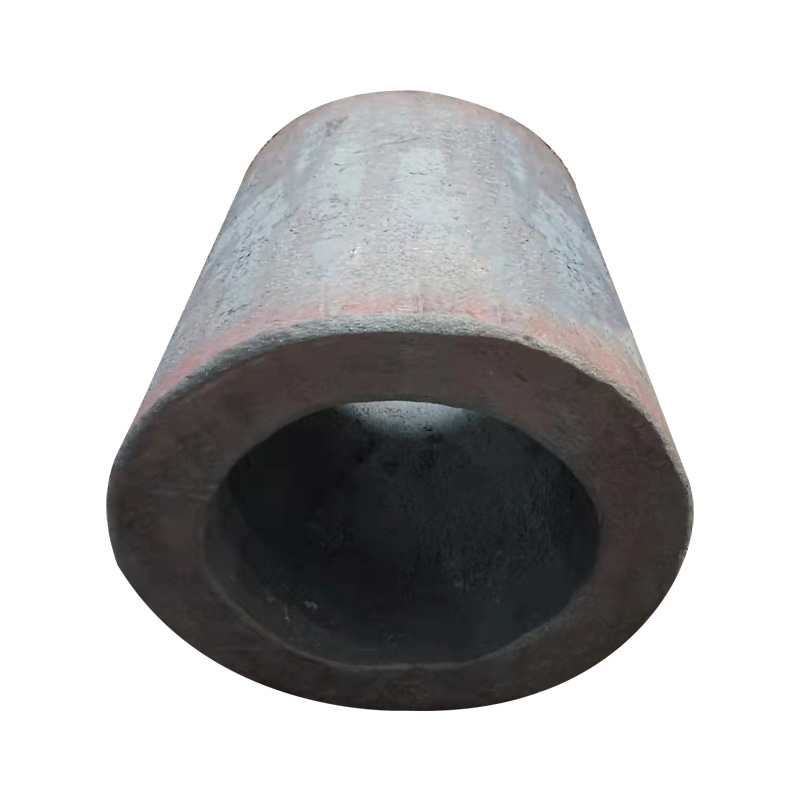