In the forging plant, improve productivity is the eternal pursuit of the goal, the forging manufacturers are committed to forging machinery high speed research, the forging manufacturers are committed to forging machinery high speed research, in the NUMERICAL control rotary head press, mainly using servo control hydraulic main drive system to improve the press stroke times.
In the pursuit of high speed processing, it is necessary to shorten production auxiliary time as much as possible in order to obtain good technical and economic benefits. The CNC press is equipped with servo motor driven 3-coordinate loading and unloading device, which can make the stamping center realize efficient sheet metal processing.
Thus several processes or several processes compound in a machine tool to complete, is currently all kinds of machine tools to greatly reduce the production of auxiliary time, improve the productivity of an important technical approach, in forging machinery has also been successfully applied, the effect is very significant. Such as: Germany, the United States, Japan has developed laser step blunt composite machine, die cutting and laser cutting organically, a workpiece feeding can complete punching, punching, flanging, shallow drawing, cutting process, utmost ground saves the auxiliary time, is particularly suited to pass multiple and complex machining of panel class and more varieties of small batch sheet metal processing. Improving the efficiency of forging processing is the primary task of forging factory, so as to have more production efficiency.
Due to the large section size of large forgings and the complex production process, the heat treatment should consider the following characteristics: the structure and properties are very uneven; Uneven grain size; Large residual stress exists; Some forgings are easy to wear white spot defects, therefore, the task of heat treatment of large forgings, in addition to eliminate stress, reduce hardness, is mainly to prevent white spots in forgings; The second is to make the forging chemical composition uniformity, adjust and refine the forging structure. The heat treatment of large forgings is usually combined with cooling after forging.
Prevent white point treatment: white point sensitive large forgings after forging cooling and heat treatment, if you can diffuse a lot of hydrogen out, while minimizing the organizational stress, you can avoid white point.
Normalizing tempering treatment: for white point insensitive steel and ingot after vacuum treatment of large forgings, because the forging will not produce white point, after forging is taken normalizing tempering treatment, so that the forging grain refinement, uniform structure.
In actual production, most forgings are normalized and tempered by hot charging furnace after forging. Air cooled forgings after forging can only be normalized and tempered in cold furnace. The purpose of undercooling after normalizing is to reduce the central temperature of the forging, so that the temperature is uniform by proper insulation, but also can play the role of hydrogen removal. The undercooling temperature varies with different types of steel, generally 350-400℃ or 400-450℃ for hot loading furnace, and 300-450℃ for cold loading furnace.
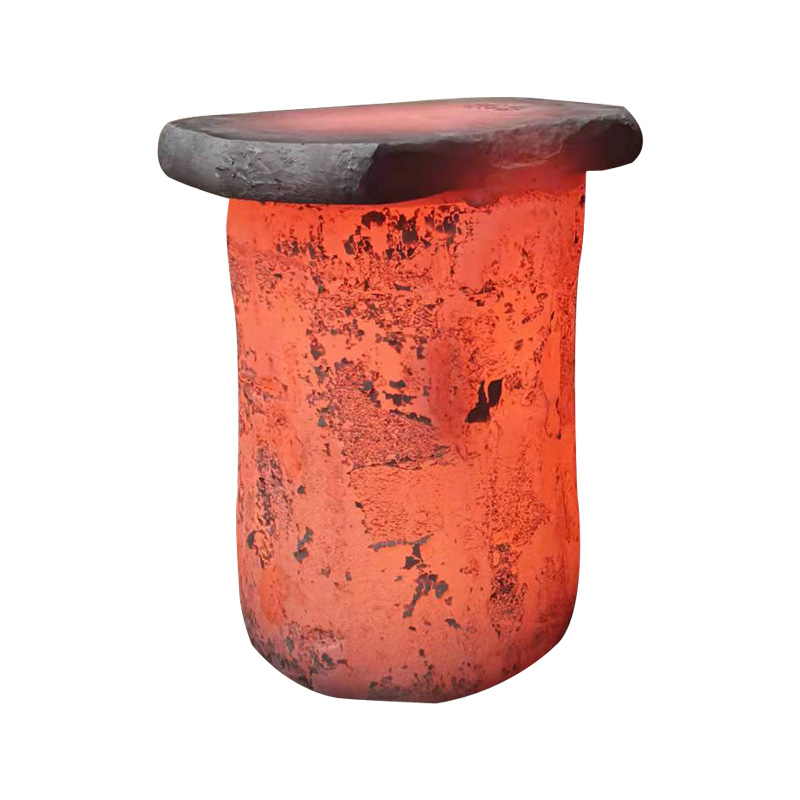